29/11/2024
Enhancing Rail Safety: The Class 153’s Innovation in Remote Track Inspection
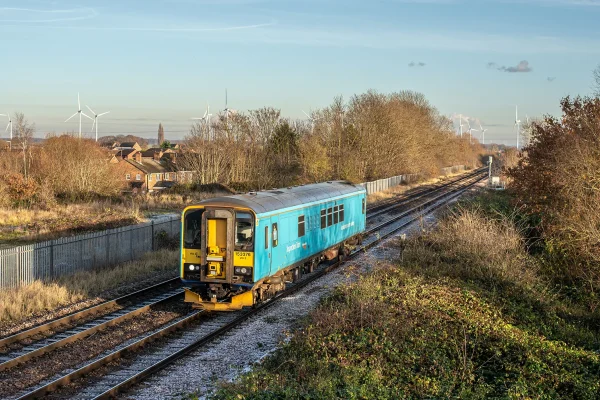
The Class 153 project is a great example of how innovative technology and cross-industry collaboration can significantly enhance rail safety and operational efficiency. The integration of AIVR and RailLoc has not only reduced the need for on-foot inspections but also enabled precise, real-time monitoring and predictive maintenance, ensuring the longevity of critical track components.
Network Rail is responsible for maintaining and renewing 20,000 miles of track across Britain, including critical components such as rails, sleepers, and switches and crossings (S&C). S&C are particularly vulnerable to wear and deformation caused by train movements, making them the highest risk asset in track engineering.
Due to their importance, Network Rail standards mandate frequent inspections, sometimes up to weekly in certain areas. Traditional inspection methods require track workers to be physically present on-site, often during night-time hours with poor lighting or during the day under possession, disrupting passenger and freight services. This not only increases safety risks for workers but also has posed challenges in completing inspections within tighter possession times. Following a series of serious incidents, there was an urgent need to improve the safety and efficiency of track inspections, leading to the development of the Class 153 Condition Monitoring train.
The Class 153 Project
In 2023, Network Rail and Porterbrook, in collaboration with multiple companies in the industry, launched the Class 153 project, a transformative initiative to modernise track inspections through remote condition monitoring for increased safety and efficiency. The project involved repurposing former 153 passenger trains with innovative technology from various industry partners such as One Big Circle (OBC) and Machines with Vision (MWV), to become Visual Inspection Units (VIUs). These trains are equipped with OBC’s high-definition cameras for forward-facing, thermal, line scanning, and structural data capture, and MWV’s RailLoc to correctly map and position all of the recorded data, and basic geometry measurement equipment.
These systems operate autonomously, capturing high-quality video inspections of S&C at line-speed. The data is then uploaded to the OBC’s AIVR Platform for online and secure analysis, allowing engineers to virtually inspect the track and detect defects from a safe, remote location. This innovation has reduced the need for on-foot inspections by up to 50%, significantly enhancing safety and efficiency, and the project’s success was recognised with the “Safety Achievement of the Year” Award at the National Rail Awards 2023.
The Class 153 VIU 2, installed with AIVR and RailLoc Technology. Photo credit: Alan Padley
AIVR (Automated Intelligent Video Review)
OBC’s AIVR technology is integral to the Class 153 project, enabling advanced remote inspection capabilities. A range of OBC’s cutting-edge data capture devices is installed on the vehicle, including systems for forward-facing video, thermal video, structural inspection video, and line-scanning imagery. Together, these tools deliver a comprehensive view of the track environment.
The AIVR Focus line-scanning system, in particular, provides high-definition imagery of the track. Utilising machine learning, AIVR automatically identifies key track components such as joints, switches, crossings, adjustment switches, welds, and railhead defects. It also highlights other critical points of interest, including potential defects, ensuring thorough and efficient track analysis.
High-Definition track image captured by AIVR Focus
RailLoc – Accurate measurement positioning you can trust
A critical part of the Class 153 solution is accurately positioning all of the data recorded by the cameras and the geometry measurement system. Traditionally this would be done with GNSS and inertial navigation but in railway applications this can lead to many metres, and even tens of metres, of positional error and sometimes assigning data to the wrong track. This would be completely unacceptable for this remote track inspection service.
MWV developed RailLoc to solve the problem of railway positioning by enhancing the traditional GNSS and inertial navigation approach with technology from the mobile robotics and autonomous driving industries. With RailLoc, every measurement is positioned to better than the current standard of one metre and data is always assigned to the correct track. In fact, RailLoc positions 95% of measurements to better than 10cm.
RailLoc uses a camera sensor, RailLoc Edge, installed onto the underside of the train looking at the track and cloud software, RailLoc Cloud, then calculates positions and provides this information, a few minutes after the train recording, for easy integration with the end application. RailLoc uses sophisticated algorithms to automatically build a map of visible track features and then uses this map to calculate the train position from the view of the track.
RailLoc installed on a Class 153
Integration of AIVR and RailLoc
As the Class 153 trains travel around the rail network, imagery from AIVR is automatically streamed to the cloud, while RailLoc Edge simultaneously captures thousands of visible track features every minute which are sent to RailLoc Cloud for processing. The direct integration between AIVR and RailLoc ensures precise location tracking for each camera—some installations feature up to 7 inspection cameras and 3 additional forward/backward cameras. This integration allows the AIVR system to request and receive the exact position of images from RailLoc Cloud in near real-time.
The processed data enables users to view up-to-date imagery from precise locations almost immediately, allowing virtual inspections of switches within minutes of a train passing. The AIVR Platform displays data from various capture systems, including the Class 153 VIU, which provides both forward-facing and underbody inspection footage.
Switch detected on the AIVR Platform, with MVW’s logo confirming the position of the switch.
Benefits of the Collaboration
Integration of AIVR and RailLoc
The primary purpose of the Class 153 project was to capture footage for conducting basic Visual Inspections (BVI) of S&C without the need for physical track patrols. To achieve comprehensive coverage, the train must execute multiple complex manoeuvres over various S&C sets. Inspectors then review the captured data using the AIVR interface. The collaboration enabled the creation of a truly innovative digital interface—a schematic, interactive version of the traditional analog patrolling diagram—that allows inspectors to easily navigate and analyse the AIVR data with a simple click, only made possible by MWV RailLoc’s precise positioning.
Faster Resolution of Defects
The precise positioning provided by RailLoc allows for reliable reporting of track defects detected by AIVR, meaning that defects and asset faults can be reliably and accurately reported to track engineers, leading to faster resolution and improved asset data quality. With the accurate positioning, OBC are able to correlate run-on-run re-detections of the same asset building an integrated model of the asset’s condition – ultimately making predictive maintenance possible through continuous condition monitoring. By accurately assessing the conditions of these assets and identifying potential ‘issues’ for further investigation, the system contributes significantly to the longevity of track components and helps in avoiding costly emergency repairs.
Even in areas where no assets or features are detected for calibration, the accurate data from MWV allows engineers to retrieve the exact position from previous runs. This capability lets them access the same image of a section of plain track that may be showing unusual behaviours or undetected defects, enabling further analysis and investigation.
“Machines with Vision and One Big Circle have been collaborating on the Class 153 project since its inception. It’s been rewarding to see the growth of AIVR and RailLoc working together. One of our goals at MWV is to see the benefits of our technology being realised by the end users, we are seeing this being achieved through this project with AIVR. We’ve worked very closely over the last few years, the open nature of both companies and the modern approach to data sharing from both sides mean that we not only provide value to each other, but together, more value to the users who need data. This type of circular collaboration will continue to unlock insight and benefits for the railway in the years ahead. It is a pleasure to be involved with OBC and AIVR.” Jonathan Owen, CTO at Machines with Vision
“The demand for remote, trusted, digital inspection capabilities is only growing, and the industry is very aware of the huge benefits that it brings to various roles, keeping people safer and trains on the move. As providers of the types of ground-breaking technologies that can help deliver this, it has been crucial to work together alongside the rail industry experts to firstly test and then rapidly deploy these combined capabilities. Working with MWV for example demonstrates that openness to collaborate for the greater good, and the ambition to deliver the services that make a difference to the end users every day.” Emily Kent, Founder at One Big Circle